CARTER DAY
Principles of the drying system
Carter Day drying system is equipped with bulk material removal and front dewatering device. It is a device that integrates the function of removing large lumps and front dewatering, mainly used in PP, PE, NYLON, EPS… and other plastic dehydration drying.
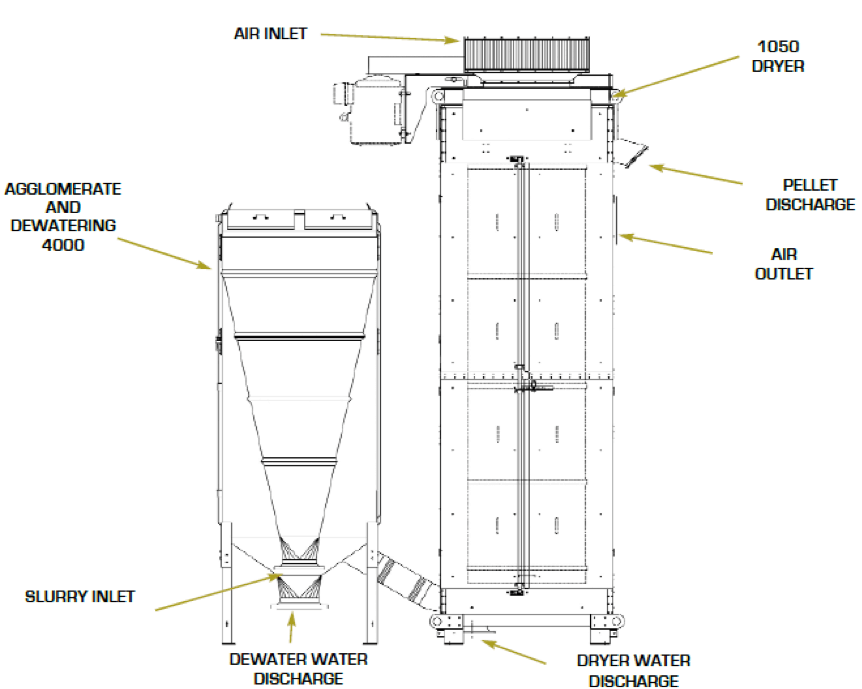
PLASTIC | PP, HDPE, LDPE & LLDPE |
SIZE MM | 2.5 x 3mm to 4×4 mm |
WATER TEMP | 60C and above |
PELLET TEMP | 60C and above |
AMBIENT TEMP | 20-45 C |
INCOMING AIR TEMP/DEW POINT | 20-40 C / 80-95% Humidity |
ADDITIVES | Slip & Non Slip |
MELT INDEX | 4 to 10 |
FINES | > 0.5% per hr. |
AGGLOMERATES | Less than 0.02% per hr |
AGGLOMERATE SIZE | 13 mm or less |
STRINGERS | Less than 0.01% per hr. |
AUDU WATER REMOVAL | 90 to 95% |
The Pellet Drying Process take place in four stages:
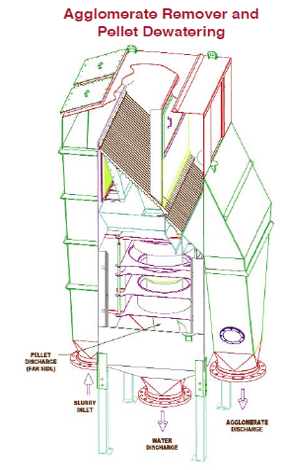
STEP 1
Agglomerate Removal
The first step in the SPINAWAY drying system is the Carter Day AUDU Dewatering System which combines the unequalled agglomerate removal and originators of vertical dewatering capabilities. The AUDU is the industry-leading agglomerate and dewatering machine with capacities matched for our 32 and 50 Series dryers.
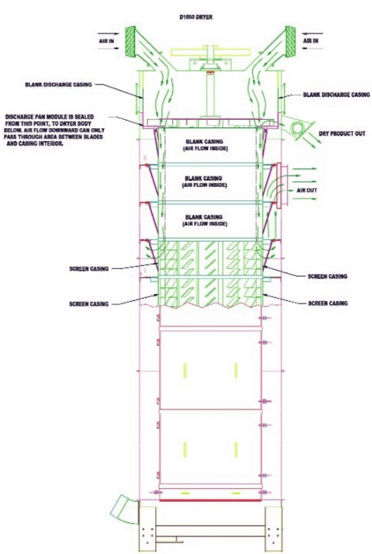
STEP 2
Dewatering
Start-up conditions within extruders and pellet cutters can produce agglomerate chunks of pellets which, if greater than 1/2 inch (12.7 mm), may cause damage to internal dryer screens and rotor. The extra wide agglomerate grid offers more surface area for difficult products. For the second step after agglomerate removal the slurry flows through a highly efficient vertical dewatering tower before going to the dryer. This design has no moving parts therefore greatly simplifying maintenance and operation.
STEP 3
SpinAway Dryer remove
The third step in high capacity pellet drying is the 32 and 50 Series Spinaway Dryer. For more than five decades serving the polyolefin industry. Carter Day’s Centrifugal Dryers have a proven record of performance dating from the 1960’s. We still service and support dryers built in that era. Carter Day’s new 50 Series SPINAWAY Drying System delivers unsurpassed dewatering and drying efficiency for pelletized plastics. The D1050 can dry plastics pellets 100,000 kg/hr and beyond.
STEP 4
Forced air
Final drying is accomplished by spinning off the moisture through the centrifugal action of the vertical rotor located in the center of the dryer. The rotor consists of impeller blades extending from the bottom to the top of the SPINAWAY Dryer. As the water is removed, pellets are carried to the top by the rotating blades.
Our tubular solid rotor design and solid casing (screen) selection allows us to control the countercurrent air flow through the pellets with none of it passing into the rotor (path of least resistance) and bypassing the pellets. This allows for improved pellet dryness. In this example we have provided additional solid casings to increase the air contact time. The product is then discharged at the top.